What Is the Difference Between Curtain Grouting and Consolidation Grouting in Houston, TX?
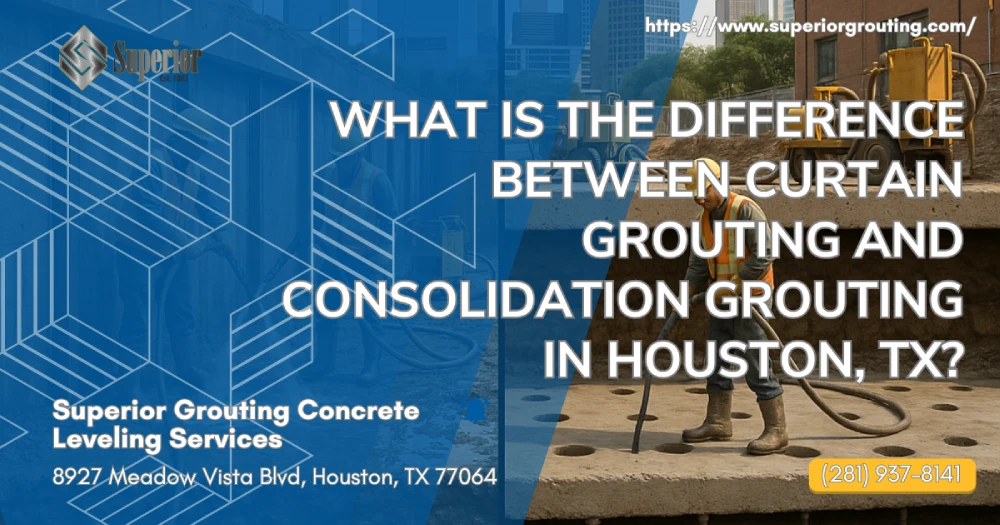
Curious about how engineers battle Houston’s swamp-born soils and sky-high groundwater? If you work around docks, levees, petrochemical facilities, or rail yards, you’ve likely heard contractors mention curtain grouting and consolidation grouting. Although both inject fluid grout underground, they solve very different problems. The elevator pitch is simple: a grout curtain stops water from bayou floods to tidal surges, while consolidation grouting beefs up weak layers so heavy structures don’t settle or tilt.
Below you’ll find a deep dive into when, why, and how each method is deployed across Southeast Texas, plus guidance on picking the right technique for your project, monitoring success, and meeting regulatory requirements.
Key Takeaways
- Curtain grouting forms a low-permeability wall that blocks subsurface seepage, protecting dams, levees, floodwalls, and cofferdams from internal erosion.
- Consolidation grouting fills voids, densifies granular layers, and strengthens fractured rock or soft clay to increase bearing capacity beneath tanks, piers, and compressor stations.
- Curtain programs drill rows of holes along the seepage path and inject cement-bentonite from the bottom up; consolidation uses discrete lenses or columns placed in weak zones.
- Grout selection differs: curtain mixes target ultra-low hydraulic conductivity, whereas consolidation mixes prioritize flowability and volume replacement.
- Houston projects must address high groundwater pressures, sulfate-rich water, expansive clays, and subsidence history—field trials and real-time monitoring are essential.
Houston’s Subsurface: Why Grouting Matters
Houston sits on a jigsaw of alluvial sand, silty clay, and organic silt laid down by countless bayou floods. Add a shallow water table and frequent storm surges, and you have an environment that challenges any foundation. Traditional cut-off walls and deep foundations help, but grouting delivers cost-effective, targeted risk reduction—especially where access is tight or structures are already in place.
Common Industrial Sites Requiring Grouting
- Ship-channel bulkheads and dry-docks
- Liquid-natural-gas (LNG) terminals
- Petrochemical process units and pipe racks
- Rail transload yards and crane railways
- Pump stations, spillways, and outlet works
Curtain Grouting Explained
Purpose
Curtain grouting (a “grout curtain”) is designed to reduce permeability. Picture a hidden dam—an underground vertical wall that forces water to choose a longer, slower path or to stop altogether. The resulting drop in flow velocity prevents internal erosion, piping, and uplift pressures that could destabilize levees or floodwalls.
Process Overview
- Site Investigation: Borehole geophysics, packer-testing, and hydraulic modeling confirm the seepage path and target depth.
- Hole Layout: Engineers design one to three rows of drill holes, often 1.5–3 m on center, offset to create overlap.
- Stage Drilling: Crews drill and case holes, installing inflatable packers that isolate modest depths (1–2 m) to control pressure.
- Grout Injection: Cement-bentonite or microfine-cement suspensions are pumped bottom-up. Pressures are logged continuously; operators watch for sudden take (indicating an open channel) or pressure spikes (a sign of hydro-fracture risk).
- Verification: Water-loss tests, vibrating wire piezometers, and borehole TV cameras confirm the curtain’s continuity and hydraulic performance.
Materials Tailored for Gulf Coast Chemistry
Houston’s groundwater often contains chlorides and sulfates. Sulfate-resistant Portland cement blended with bentonite, slag, or fly ash resists chemical attack. Microfine cement particles—6–10 µm—let grout invade tiny sand pores and tight fracture networks.
Performance Metrics
- Hydraulic Conductivity: An order-of-magnitude drop is typical (e.g., from 1 × 10⁻⁵ cm/s to 1 × 10⁻⁶ cm/s).
- Piezometric Head: Upstream-to-downstream head differential stabilizes after installation.
- Grout Take Curve: Consistent taper toward refusal shows voids are filled without excessive waste or blowout.
Consolidation Grouting Explained
Purpose
Consolidation grouting boosts soil or rock strength and stiffness, controlling settlement and increasing allowable bearing pressure. Instead of forming a continuous wall, the grout forms discrete bulbs that bond loose grains, close joints, and compact voids.
Ideal Settings in Harris County
- Reclaimed dredge spoil beneath tank farms
- Fractured clay lenses under rail spurs
- Soft Beaumont clay supporting compressor skids
- Sand channels threatening differential settlement beneath pipe racks
Injection Strategy
- Stage Depths: 5–20 ft intervals based on lithology.
- Pressure Window: Typically 100–300 psi—enough to fracture and permeate, yet below uplift or heave thresholds.
- Volume Criteria: 5–25 gal/ft, ending when pressure sharply rises or predetermined refusal is met.
- Pattern: Triangular, square, or radial patterns concentrate on mapped weak zones, not continuous lines.
Strength Gains
A well-executed program can double SPT N-values, boost CPT tip resistance, and trim post-construction settlement by 50 % or more. For large rotating equipment or precision-aligned process units, that margin keeps maintenance budgets in check.
QA/QC
- Heave Pins & Settlement Points track surface movement.
- Downhole Pressure Cells verify distribution and prevent over-pressurization.
- Post-grout CPT, pressuremeter, or coring documents the increased modulus and grout penetration.
Curtain vs. Consolidation: Fast Comparison
Aspect | Curtain Grouting | Consolidation Grouting |
Core Objective | Seepage cutoff | Strength & settlement control |
Geometry | Continuous vertical barrier | Discrete bulbs or columns |
Typical Mix | Cement-bentonite, microfine cement | High-flow cement, microfine, or chemical |
Verification Focus | Permeability reduction | Modulus & strength increase |
Common Houston Applications | Dams, levees, cofferdams | Tank pads, pipe racks, heavy modules |
Key Risk | Hydro-fracturing & blowout | Uplift or surface heave |
Selecting the Right Technique for Your Project
Decision Drivers
- Hydrogeology: High heads and open seepage pathways? A curtain is mandatory.
- Structural Demands: Heavy vertical loads on compressible soil? Consolidation fits the bill.
- Access & Schedule: Curtain programs can be linear and longer, whereas consolidation gear can slot into tight work windows between shutdowns.
- Budget: Material and drilling footage often push curtain costs higher; consolidation may offer a smaller footprint and faster return to service.
- Regulatory Requirements: Texas Water Development Board dam-safety rules lean toward curtains; Texas Commission on Environmental Quality focuses on environmental containment as well.
Hybrid Programs
Some waterfront pump stations combine a shallow curtain (stopping bayou water) with deep consolidation columns beneath pump pedestals, yielding a balanced system that controls uplift and settlement simultaneously.
Environmental & Safety Considerations
- Spoil Management: Returned slurry must be captured in lined cells per TPWD guidelines.
- Worker Safety: High-pressure lines, cement silos, and chemical admixtures require respiratory protection, splash guards, and confined-space protocols.
- Community Impact: Noise-shielded drill rigs and low-odor admixtures keep nearby businesses running without complaint.
Real-World Snapshot: Ship Channel Floodwall Upgrade
A recent floodwall retrofit along the Houston Ship Channel needed both methods. Engineers first installed a 90-ft-deep cement-bentonite curtain to cut off seepage beneath the sheet-pile wall. Once piezometers confirmed the water table drop, crews switched to consolidation grouting under crane rails, densifying the soft dredge spoil that threatened track alignment. The dual program shaved six weeks off the schedule versus a traditional diaphragm wall and saved 18 % in total cost.
Maintenance and Longevity
Properly installed grout curtains and consolidation bulbs can perform for decades. Routine inspections—visual, piezometric, and settlement monitoring—spot early warning signs. In aggressive sulfate environments, blended cements and supplementary cementitious materials (SCMs) extend service life. Should performance taper off, secondary grouting often rejuvenates the system with minimal downtime.
Conclusion
Curtain grouting and consolidation grouting may share pumps, mixers, and crews, but their missions diverge: curtain grouting stops water, and consolidation grouting strengthens soil. Matching the technique to site conditions, structural demands, and Houston’s unique hydrogeology keeps infrastructure safe and compliant. Partner with an experienced contractor, like Superior Grouting, to tailor a data-driven solution and secure long-term performance.
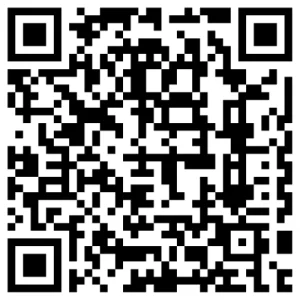