What Is Grouting as a Stabilization Method in Houston, TX?
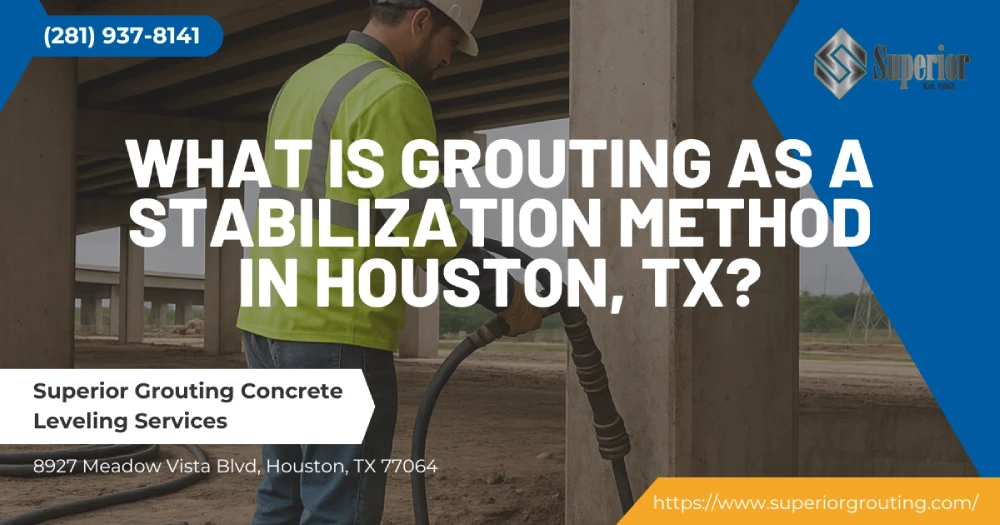
Houston’s fast-growing industrial corridor sits on soft, moisture-sensitive Gulf Coast soils. When heavy structures, pipelines, or transportation hubs are built on these layers, voids form, loads shift, and differential settlement follows. Grouting—an essential technique in geotechnical engineering—offers a cost-effective solution that fills voids, compacts loose soil, and dramatically improves long-term stability without massive excavation.
Below, discover how our grouting solutions can support your next project and why Superior Grouting Services in TX remains the preferred partner for complex ground stabilization.
Key Takeaways
- Grouting strengthens weak Gulf Coast soils by injecting cement or polyurethane into voids, compacting loose layers, and boosting load-bearing capacity—offering a non-invasive, cost-effective stabilization solution for Houston’s industrial and infrastructure development needs.
- Polyurethane grouting expands rapidly to fill gaps, seal leaks, and lift slabs without adding significant weight, making it an ideal choice for saturated soils, limited-access sites, and time-sensitive stabilization projects across the Houston area.
- Compaction and permeation grouting improve structural reliability by densifying unstable soil zones and sealing porous ground, helping prevent settlement, support heavy loads, and extend the lifespan of assets like slabs, tanks, and transportation corridors.
- Grouting reduces erosion threats by forming a cohesive, water-resistant mass within the soil, blocking seepage paths and protecting floodwalls, marine structures, and critical utilities from damage during storm surges and fluctuating groundwater conditions.
- The choice of grout—cement, polyurethane, or chemical—depends on specific site conditions, required strength, groundwater presence, and structural goals, with each formulation tailored by Superior Grouting for maximum performance and cost-efficiency.
- Superior Grouting ensures consistent results through site-specific mix designs, real-time QA tracking, and experienced field crews, supporting Houston’s demanding construction projects with fast mobilization, minimal disruption, and long-term soil stabilization.
Grouting: An Essential Ground Stabilization Technique on the Gulf Coast
Grouting involves injecting a fluid—or sometimes thixotropic—mixture into the soil under pressure. That mixture, called grout, hardens into a solid mass that reinforces weak strata, seals leaks, and arrests settlement. Pressure grouting involves controlled pumps, monitoring gauges, and a tailored blend of cement, polyurethane foam, or chemical resin. By manipulating viscosity, set time, and flow rate, engineers achieve precise ground stabilization across diverse Houston construction sites.
Soil Challenges in Houston
The surface geology around the Houston Ship Channel alternates between compressible clays, water-bearing sands, and organic silts. Such soft soil suffers rapid consolidation, low shear strength, and elevated erosion potential when storms strike. A reliable method to stabilize soil must:
Increase the soil’s load-bearing capacity so slabs, tanks, and bridge approaches remain level.
Shut down seepage paths that accelerate soil erosion and undermine infrastructure.
Function despite high groundwater and tight project footprints.
Grouting in Houston accomplishes all three by forming a dense, water-resistant matrix that limits movement and strengthens the underlying soil particles.
Grout Materials: From Cement to Polyurethane
Not all grouts behave the same; selection hinges on project goals, ground conditions, and access.
- Cement Grouting – Portland cement, slag, or micro-fine blends permeate medium sands and fill voids behind bulkheads. Cement grouting is primarily used to moderate permeability and upgrade bearing capacity.
- Polyurethane – A two-part polyurethane resin expands into polyfoam, displaces water, and bonds soil grains. Because polyurethane grouting weighs far less than cement, it adds minimal load while sealing leaks in tunnels or culverts.
- Chemical Grouts – Sodium silicate or acrylate solutions permeate fine sands and cure into a flexible gel ideal for leak sealing around sheet-piling joints.
- Hybrid Mixes – On some projects, Superior Grouting injects a staged sequence—low-viscosity chemical grout first, followed by compaction grout—to maximize both waterproofing and structural gain.
Polyurethane Grouting: Lightweight Powerhouse
When ground saturation is high and access is limited, polyurethane grouting stands out. The resin foams up to 30 times its liquid volume, filling every gap in the soil, lifting concrete slabs, and stabilizing voids beneath critical equipment pads. Because the cured polyfoam is chemically inert and water-resistant, it maintains performance during Houston’s seasonal floods.
Key benefits:
- Minimal added weight on unstable soil.
- Fast reaction times—facility shutdowns measured in hours, not days.
- Superior adhesion to concrete slabs and steel sheet piles.
- Excellent leak sealing in manholes, joints, and below-grade utilities.
Boosting Bearing Capacity Through Strategic Injection
Heavy industrial modules demand ground capable of supporting high live and dead loads. Injection grouting strengthens weak zones, transfers stress to competent strata, and raises overall bearing capacity by as much as 300 percent. Compaction grouting uses a stiff, low-mobility mix that forms bulbs, compacts loose soil, and prevents further settlement. The result is a uniform, capable foundation that limits maintenance costs over the asset’s lifespan.
Managing Erosion and Soil Erosion Risks
Erosion threatens embankments, floodwalls, and wharf structures across the Gulf Coast. Grouting serves as an effective method to seal erodible layers, create cutoff walls, and protect against piping failure. By consolidating soil particles into a cohesive mass, grout disrupts water pathways and inhibits soil erosion even during tropical storm surges.
Selecting the Right Grouts for Every Construction Site
Superior Grouting follows a data-driven approach:
- Site Investigation – Cone penetration tests reveal loose soil lenses needing reinforcement.
- Laboratory Mix Design – We adjust water-cement ratio, accelerators, and fly ash to match site chemistry.
- Field Verification – Pressure, volume, and grout spread are tracked in real time to confirm that the grout is injected exactly where planned.
This rigorous process ensures the selected grouts perform as specified, whether we’re executing jet grouting below a rail spur or permeation grouting beneath a petrochemical tank farm.
Project Workflow: From Site Investigation to Final Verification
- Geotechnical Characterization – Boreholes, piezometers, and pressuremeter testing establish native soil properties.
- Design Phase – Engineers model load paths, predict displacement, and specify injection pressures.
- Pilot Section – A test panel validates grout take, set times, and reinforces quality benchmarks.
- Full-Scale Injection – Low-vibration drilling patterns and staged pumping prevent heave while achieving target compaction.
- Post-Grout Verification – Coring, ground-penetrating radar, and settlement monitoring confirm results meet contract tolerances.
Comparing Compaction, Jet, and Permeation Grouting
- Compaction Grouting – Displaces and compacts loose soils, raises foundations, and stabilizes voids. Best for increasing load-bearing capacity beneath slab or structure foundations.
- Jet Grouting – High-velocity jets create soil-cement columns ideal for floodwall toes, cofferdam cutoffs, and underpinning. Diameter and strength are adjustable for complex infrastructure projects.
- Permeation Grouting – Low-viscosity grout permeates pores without ground heave, an effective approach for seepage control around docks or pipeline crossings.
Each technique is a solid choice; selection depends on soil type, allowable displacement, and project schedule.
Cost, Schedule, and ESG Benefits
Grouting solutions often outpace deep foundations or mass excavation in both time and money:
- Rapid Mobilization – Small rig footprints reduce site congestion.
- Limited Spoils – No massive haul-off of excavated soil, lowering disposal fees.
- ESG Alignment – Sealed soil prevents contaminant migration and protects nearby wetlands, aligning with corporate sustainability metrics.
- Reduced Downtime – Facilities remain operational while Superior Grouting crews work below grade.
Why Superior Grouting Services in TX Stand Out
Superior Grouting has delivered compaction grouting, permeation grouting, and polyurethane slab leveling across Houston for more than three decades. Our fleet of high-pressure pumps, mobile mixing labs, and cloud-based QA/QC dashboards guarantees each injection meets or exceeds project specifications. From leak sealing at petrochemical docks to stabilizing unstable soil beneath rail corridors, our superior grouting concrete leveling services keep critical infrastructure safe, level, and capable of supporting heavy industrial loads.
How Our Grouting Solutions Can Support Your Next Project
Planning a pipeline expansion, LNG facility, or Port of Houston upgrade? Superior Grouting concrete leveling specialists analyze site data, recommend the most cost-effective solution, and execute the work under strict safety and environmental controls. Whether the challenge involves injecting polyurethane foam to lift slabs, cement grouting to fill voids, or jet grouting to underpin soft soil, our experienced crews provide the stabilization and peace of mind that your team demands.
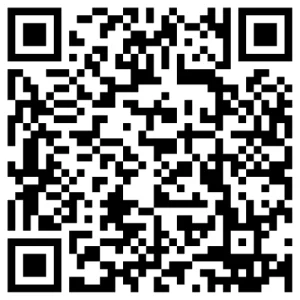