Is Foam Concrete the Same as Aerated Concrete in Beaumont, TX?
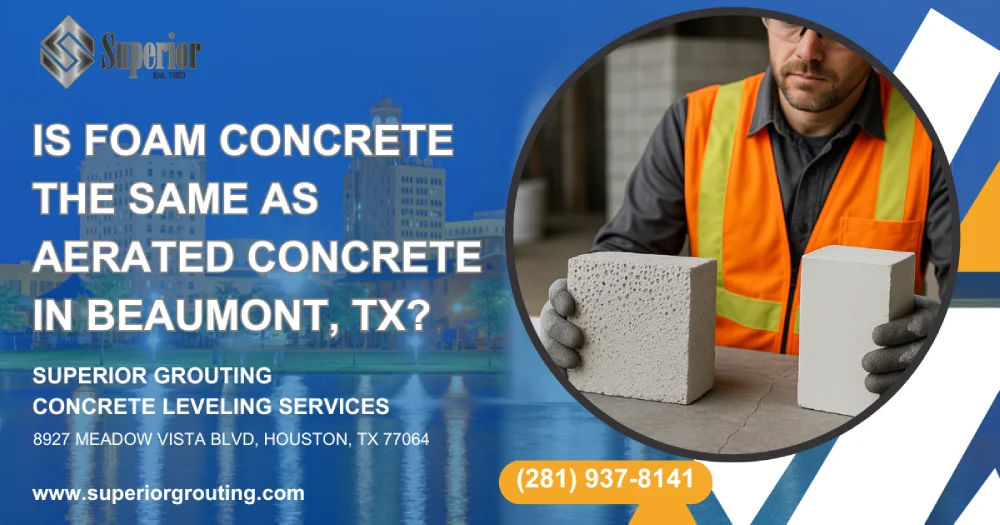
Foam concrete, also known as aircrete, and aerated concrete share the same lightweight DNA, yet the methods that create their signature air bubbles differ. Both materials are prized across Beaumont, TX for industrial projects that demand reduced density, solid thermal insulation, and quick turnaround times that minimize downtime costs at refineries, loading docks, and heavy‐haul corridors. In this guide we clarify the chemistry, compare density and compressive strength numbers to conventional concrete, and show where foam-based leveling services outperform high-density cement grout or polyurethane foam alone.
Key Takeaways
- Foam and aerated concrete differ in production methods but share benefits like low density, high thermal insulation, and fast installation—ideal for Beaumont’s industrial builds and Gulf Coast climates.
- Foam concrete cures without autoclaving, making it perfect for on-site grouting and slab leveling where speed and pumpability are crucial for minimizing downtime in active refinery and warehouse environments.
- Cellular mixes offer strength and vapor control, achieving up to 2,000 psi and resisting Gulf humidity through a breathable matrix that protects coatings and improves performance under heavy equipment loads.
- Combining polyurethane foam with foam concrete provides both immediate lift and long-term void stability, giving Beaumont contractors the flexibility to level floors without removing machinery or halting operations.
- Proper mix design and surface prep are critical to ensure foam concrete meets industrial standards for load-bearing strength, shear resistance, and thermal performance in Southeast Texas’ demanding conditions.
Beaumont, TX Contractors Ask: Is Foam Concrete Structural?
Lightweight doesn’t automatically mean non-structural. Properly designed cellular lightweight concrete (CLC) mixes can achieve 1,500 psi, enough to handle many load-bearing industrial slabs and pipe racks. When higher strengths are required—say under a rail spur or turbine pad—engineers can specify:
- Lower water-cement ratios
- Class F fly ash or slag in the cementitious blend
- High-shear mixing to distribute a uniform closed-cell bubble network
Because the void structure is predictable, cellular concrete resists settlement better than expansive soils under normal-weight concrete. In Beaumont’s sulfatic clays, reducing overburden can add decades to a foundation’s service life.
How Air Bubbles Are Formed: Foaming Agent vs. Autoclave
- Foam Concrete (Non-Autoclaved)
A protein or synthetic foaming agent is whipped with water to produce a shaving-cream consistency. This foam is injected into a cement-sand slurry, creating millions of tiny, stable bubbles. Curing happens at ambient temperatures—no autoclave is needed—making the process ideal for on-site bulk grouting or floor leveling in Beaumont refineries where continuous pours are common. - Aerated Concrete (Autoclaved)
Fine aluminum powder reacts with calcium hydroxide, releasing hydrogen gas that inflates the mix. Large molds are then steamed at 180 °C in an autoclave, which locks in higher strengths than non-autoclaved material. The final product is factory-cut into blocks or panels used for roof decks, blast walls, and insulated enclosure systems.
Lightweight Concrete vs. Conventional Concrete: Key Numbers
- Typical low density range: 20–80 lb/ft³ versus 145 lb/ft³ for conventional concrete
- Compressive strength: 150–2,000 psi compared to 3,000–5,000 psi normal mixes
- Thermal R-value: 0.7–1.2 per inch—roughly ten times higher than standard slurry
- Pump pressures: up to 70 % lower, enabling long horizontal or vertical runs without booster stations
Even though foam concrete is also a cement-based material, its lightweight profile reduces pile counts, shear forces on deep clays, and crane picks on modular jobsites.
Industrial Advantages in Beaumont’s Climate
- High Humidity & Vapor Drive
The cellular matrix breathes, reducing trapped moisture under epoxy coatings. A thin vapor-permeable seal keeps the surface from absorbing petrochemical spills. - Expansive Clays
Lighter fills generate lower shear stresses, making foundation repair and grout underpinning simpler when jacking settled columns or equipment pads. - Hurricane Resilience
Lower mass means less inertial loading during high-wind events. Cellular mixes used as backfill behind sheet-pile walls around a refinery channel can cut overturning moments by up to 30 %.
Where Polyurethane Foam Still Excels
While foam concrete handles high-volume voids, polyurethane—especially high-density closed-cell polyurethane foam—is unmatched for pinpoint lifting where tight tolerances matter:
- Releveling a precision mill table without shutting down adjacent lines
- Sealing slab joints at freezer docks where temperature swings create condensation
- Injecting beneath a concrete surface that must return to service within one hour
Many contractors (including Corsair Concrete Lifting) combine poly concrete leveling with cellular grouting. Polyurethane provides immediate strength, then foam concrete infills the remaining void to deliver bulk stability at a lower material cost.
Leveling Services That Combine Foam Concrete and Poly Concrete
A typical industrial floor leveling service sequence in Beaumont might look like this:
- Core-drill ⅝-in. ports through the concrete slab around the settled area.
- Inject two-part polyurethane to raise the slab within ⅛ in. of grade.
- Follow with a pump of cellular cement slurry to back-support the entire footprint.
- Finish with rapid-set mortar or low-shrink shotcrete at surface spalls.
Compared to traditional slab replacement, multi-material lifting reduces downtime costs by 70 % and eliminates the need to remove heavy machinery.
Mix Design & Quality-Control Essentials
- Specify wet density to ±3 lb/ft³ and test per ASTM C138.
- Require 28-day cylinders under ASTM C495 for non-autoclaved mixes.
- Confirm bubble stability with a 1-hour spread test—critical in Gulf Coast heat.
- Use a minimum 30 % pozzolan replacement to resist chloride attack in marine terminals.
A proper mix design paired with rigorous cure monitoring ensures that lightweight grouts perform comparably to normal concrete in long-term durability.
Common Industrial Applications
- Grouting and sliplining abandoned utility tunnels
- Low-stress fill beneath large format roof decks at distribution hubs
- Backfill behind quay walls along the Neches River port expansion
- Blast-resistant cladding systems around refinery units
- Rapid rebuild of loading docks after sub-grade washouts
- Shotcrete repairs where cellular concrete sticks to overhead surfaces
Foam Concrete vs. Other Materials
- Concrete vs. traditional flowable fill: cellular mixes weigh 65 % less.
- Foam concrete vs. polyurethane foam: foam concrete wins on volume cost; polyurethane wins on speed and pinpoint control.
- Cellular concrete vs. cement grout: increased insulation properties and reduced bleed water make cellular mixes easier to place under sensitive equipment.
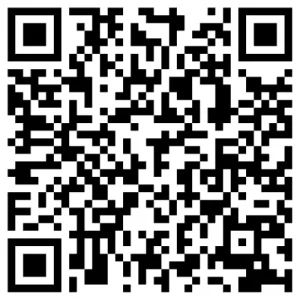