Does Concrete Leveling Really Work in Beaumont, TX?
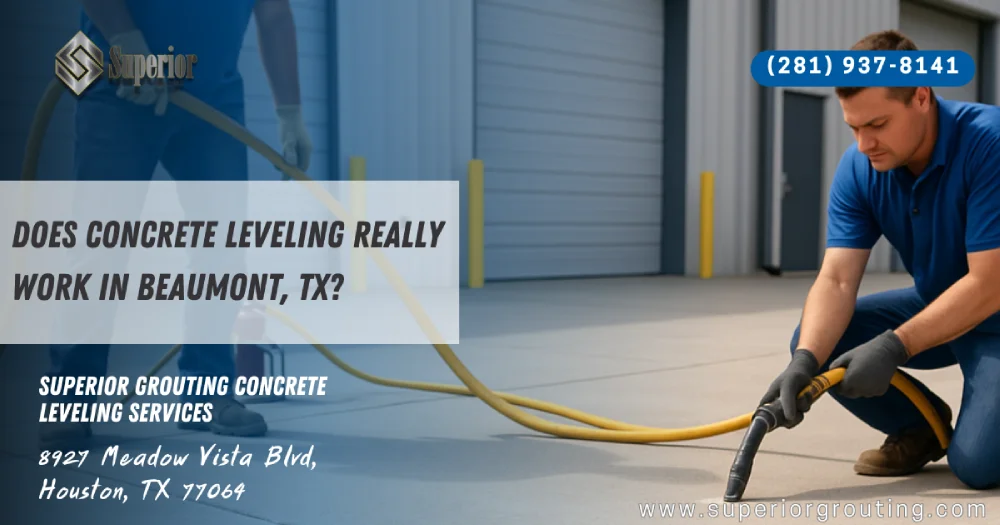
Concrete surfaces across Beaumont and Houston, TX endure heavy industrial traffic, high rainfall, and clay-rich soils that expand and shrink. Over time, slabs settle, trip hazards appear, and operations slow. Modern concrete leveling—sometimes called poly concrete leveling, poly concrete raising, slab jacking, or mudjacking—returns those slabs to grade quickly while protecting the structural integrity of adjoining foundations, piers, and equipment pads.
Below you’ll find a detailed look at how professional levelers approach a commercial or municipal leveling project, what permits and inspections are required in Jefferson County, and why Superior Grouting’s quality craftsmanship saves facility managers thousands of dollars compared with full replacement.
Key Takeaways
- Poly concrete leveling in Beaumont, TX restores uneven slabs fast, using lightweight, water-resistant foam that cures quickly and avoids overloading unstable Gulf Coast subgrades.
- The process costs 50–70% less than slab replacement, helping commercial and municipal clients reduce downtime, preserve capital, and eliminate the need to relocate inventory or shut down operations.
- Foam injection cures in 15 minutes, allowing forklifts, trailers, and production teams to resume activity the same day, minimizing disruption in high-traffic or sensitive industrial environments.
- Beaumont requires permits for public and structural work, and top contractors like Superior Grouting manage code compliance, inspections, and engineering documents to ensure a safe and legal lift.
- Warning signs like trip hazards and patio voids signal the need for leveling, which protects assets, supports safety compliance, and prevents more expensive structural damage down the road.
- Superior Grouting offers expert inspections, transparent quotes, and long-term warranties, delivering concrete leveling services that meet industrial-grade standards for precision, professionalism, and reliability.
Why Slabs Settle in Southeast Texas
- Expansive clay soils swell during wet seasons and shrink in droughts, creating voids.
- Constant axle loads on warehouse floors and refinery driveways pound unsupported panels until they sink.
- Poor drainage concentrates water beneath the concrete slab, washing away base material.
- Aging joints allow runoff to seep under the floor and crawl space beneath elevated decks, undermining the foundation.
These conditions lead to cracks, uneven transitions, and other signs of foundation distress. Early detection keeps minor movement from turning into structural damage that forces major shutdowns.
Concrete Leveling vs. Full Foundation Repair
Foundation repair companies often recommend piers or pilings when deep settlement jeopardizes a building’s load path. Yet many situations involve only the surface slab or sidewalk. Concrete leveling targets that surface layer, lifting it back to its original elevation without disturbing columns, grade beams, or anchor bolts.
Key comparisons:
- Time: Most leveling solutions are complete in hours, whereas large-scale foundation repair services can stretch for weeks.
- Cost: A leveling project is typically 50–70 % less than demolition and repour, preserving capital for other upgrades.
- Downtime: Forklift lanes, loading docks, even airport aprons can reopen the same day—a major boost to customer service metrics and safety ratings.
Step-by-Step Leveling Procedure
- Inspection & Consultation
A licensed contractor performs a laser survey, photographs every crack, and checks for additional foundation problems. This professional assessment—often delivered as a free estimate or free quote—lets stakeholders make informed decisions. - Permit & Utility Clearance
Beaumont requires a right-of-way permit for public sidewalks and a structural permit for interior industrial floors. Levelers call 811 to mark gas, water, and fiber before drilling port holes. - Drill Injection Ports
Crews drill ⅝- to 1½-inch holes in a grid pattern. Precise drilling keeps the concrete surface intact and minimizes cosmetic patching. - Foam or Slurry Injection
High-density polyurethane foam expands to fill voids, then gently lifts the slab. The lightweight foam adds no meaningful load to weak sub-grade, unlike heavy cement slurry. Real-time lasers verify each lift to the millimeter. - Patch & Finish
Ports are plugged with non-shrink grout color-matched to the existing concrete. Most floors, patios, and sidewalks can handle forklift traffic within 30 minutes. - Final Walk-Through & Warranty
Technicians document elevations, provide a written warranty that covers future settlement, and explain routine drainage maintenance that helps the slab stay level for years of experience to come.
Material Choices: Foam vs. Mudjacking Slurry
- Foam (Poly Concrete Leveling) – Closed-cell, water-resistant, and cures in 15 minutes. Ideal for interior floors, crawl spaces, and high-precision applications such as crane rails.
- Traditional Mudjacking – Sand-cement slurry is heavier and requires larger holes but excels beneath thick highway panels or rock-crushing pads.
- Hybrid Polymers – Offer the rapid cure of foam with extra compressive strength for exceptional loading scenarios.
Leading contractors, including Corsair Concrete Lifting and Superior Grouting, choose the formulation only after a thorough inspection to match site conditions.
Cost Drivers and Budget Planning
- Square Footage & Depth of Void – More void equals more material.
- Accessibility – Tight refinery corridors or elevated dock aprons may need specialized rigs.
- Concrete Thickness – Thicker slabs require additional ports and foam volume.
- Permit Fees & Engineering – Structural reviews add marginal cost but safeguard professionalism.
Average range in Beaumont TX: $4–$8 per sq ft for foam, slightly lower for slurry. A 10,000 sq ft warehouse floor that would cost $200,000 to replace might level for under $60,000—saving well over thousands of dollars while avoiding inventory relocation.
Regional Case Study
A petrochemical plant outside Lake Charles LA noticed forklift operators feeling a “trip” bump entering Tank Farm 3. Laser inspection revealed a 1.75-inch drop over a 40-ft stretch. Superior Grouting drilled 64 ports, injected foam, and restored grade overnight. Production resumed before shift change, and the client praised the top-notch workmanship and responsive customer service in their Better Business Bureau rating.
Maintenance Tips After Leveling
- Seal Expansion Joints – Prevent water infiltration.
- Improve Drainage Slopes – Direct runoff away from the slab and foundation.
- Annual Inspection – A quick laser check confirms the floor, driveway, or sidewalk remains true.
- Load Management – Distribute stacked pallets and rigs to avoid point loads that can sink isolated sections.
Following these steps honors the warranty, sustains the investment, and upholds the professionalism that your stakeholders expect.
Choosing a Contractor You Can Trust
Look for these indicators of expertise:
- Proven portfolio of industrial or municipal concrete leveling jobs in Beaumont TX, Houston, TX, and surrounding corridors.
- Active memberships and high rating in industry associations plus the Better Business Bureau.
- Transparent quote documents outlining scope, safety plan, and warranty terms.
- On-staff structural engineers who consult on complicated foundation issues.
- Commitment to quality craftsmanship, punctual schedules, and clear communication—all hallmarks of top-rated concrete contractors.
Superior Grouting meets those standards and invites you to schedule a no-obligation consultation today.
Signs You Need Concrete Leveling
- Cracks that widen or run through control joints
- Uneven joints causing a trip hazard
- Doors or dock plates that drag on the slab
- Standing water near the foundation after storms
- Visible voids under the edge of a patio or sidewalk
- Tilted machine bases indicating structural misalignment
Addressing these warning signs early prevents severe foundation repair later, maintains OSHA compliance, and protects equipment worth millions.
Bottom Line
Concrete leveling is a proven, engineered answer to uneven slab dilemmas in Beaumont TX and across Southeast Louisiana. Whether foam-based or traditional mudjacking, the process restores grade swiftly, supports structural loads, and preserves budgets. From the first inspection to final drill-hole patch, a top-rated concrete contractor demonstrates professionalism, safety, and quality workmanship that keeps operations running smoothly—helping facility owners (and yes, even information-hungry readers who are homeowners) understand how to safeguard their assets.
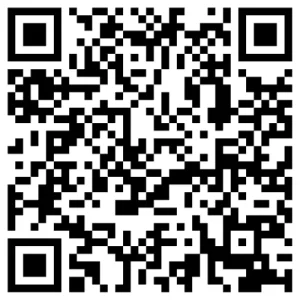