Does Self-Leveling Concrete Crack Over Time in Beaumont, TX?
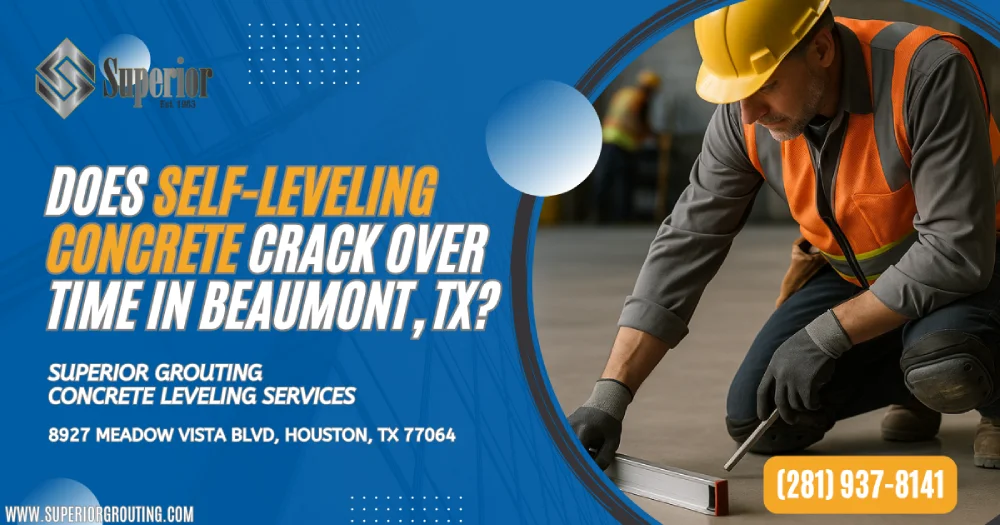
Self-leveling compounds have become the go-to solution for eliminating low spots and delivering a smooth finish on large commercial slabs from Beaumont, TX to Lake Charles, LA. Yet facility managers still ask a familiar question: “Will that mirror-flat surface stay intact, or will hairline fractures show up later?” The short answer is that properly installed self-leveling concrete rarely cracks. The longer answer—which matters across southeast Texas and southwest Louisiana—depends on moisture management, thermal movement, and the repair techniques you choose if something does go wrong.
Below, we examine why Gulf Coast environmental factors pose unique challenges, compare concrete leveling methods such as polyurethane foam injection and classic mudjacking, and outline proven maintenance tips that extend the lifespan of high-traffic concrete surfaces.
Key Takeaways
- Self-leveling concrete will not crack prematurely when moisture, temperature, and joint design are controlled.
- Beaumont’s humid climate magnifies every small mistake; strict adherence to ASTM and ACI guidelines is essential for structural integrity.
- Polyurethane foam injection frequently outperforms mudjacking for industrial facilities that can’t afford extended downtime.
- Routine maintenance—especially proper drainage and proactive sealing—prevents minor surface defects from escalating into major structural issues.
Have an uneven surface, a spalling dock slab, or a section of concrete slab that must meet tight flatness tolerances? Superior Grouting’s leveling services keep your operation running safely and smoothly throughout the Gulf Coast.
Why Gulf Coast Climate Raises the Stakes for Concrete Leveling
Beaumont sits in a humid, clay-rich zone just off the Gulf of Mexico, while neighboring industrial hubs. share similar soil and weather profiles. Constant moisture, frequent freeze-thaw cycles in winter, and scorching summer heat put every concrete slab under non-stop stress. If vapor pressure, poor drainage, or sudden temperature swings exert enough tensile force, even a robust self-leveling layer can craze or spall.
- High humidity drives moisture up through existing concrete, challenging the bonding agent that keeps the surface layer attached.
- Clay soils expand and contract dramatically, jeopardizing structural integrity if pier-and-beam supports or deep foundations are not properly engineered.
- Storm events push water under slabs, and without proper drainage—think French drains or positive site grading—future problems such as slab lift or joint separation can develop.
Common Sources of Cracking in Self-Leveling Slabs
- Excess substrate moisture (RH > 75 %)
- Thermal expansion beyond load requirements
- Inadequate joint sealing around columns and doorways
- Over-watering the grout or polymer mix
- Rapid surface drying that produces differential shrinkage
- Heavy point loads in high-traffic areas before the overlay gains full strength
- Spalling caused by de-icing salts or chemical attack in industrial environments
Each issue can be amplified in Beaumont, TX because the Gulf Coast rarely enjoys the steady, moderate climate that inland regions take for granted.
Evaluating an Existing Concrete Surface
A thorough evaluation and repair plan starts with ASTM F2170 RH testing, core sampling, and laser profiling to reveal uneven surfaces. Once data is collected, engineers can select the optimal repair process:
- Self-leveling compounds for moderate low spots (< 1″).
- Poly concrete raising or polyurethane foam injection when large voids exist under the slab.
- Traditional mudjacking (cement-based grout) for massive, exterior slabs that must resist extreme load requirements.
Polyurethane Foam Injection vs. Mudjacking vs. Slab Jacking
Technique | Material | Typical Use | Pros | Cons |
Polyurethane Foam Injection | Expanding closed-cell foam | Interior slabs, high-traffic areas | Fast cure; lightweight; minimal downtime | Higher material cost |
Mudjacking | Cementitious grout | Driveway or dock slabs | Lower cost; familiar to crews | Heavy; may settle again; longer cure |
Slab Jacking with Flowable Fill | Sand-cement slurry | Large industrial pads | Adds strength; fills big voids | Requires heavy equipment; longer shutdown |
Foam injection is particularly attractive for Beaumont foundation repair in active plants because forklifts can return to service within hours, curbing costly production delays.
Proper Installation Steps That Prevent Future Problems
- Surface profile the existing concrete to CSP 3-5 and vacuum away dust.
- Apply a manufacturer-approved primer so self-leveling products chemically bond to the slab.
- Mix using exact water-to-powder ratios; extra water weakens tensile capacity and promotes spalling.
- Maintain ambient temperatures between 65 °F and 85 °F and relative humidity below 70 % during placement.
- Use spike rollers to release trapped air, avoiding pinholes that become stress risers.
- Install control joints at 12- to 15-foot intervals and ensure joint sealing happens before traffic returns.
Maintenance Tips to Extend the Lifespan of Level Concrete
- Schedule regular cleaning with pH-neutral detergents; abrasive grit on forklift tires can gouge the surface layer.
- Reseal exposed concrete every two to three years to block oil, salt, and chemical ingress.
- Monitor crawls and voids for signs of differential movement; early detection keeps repair costs low.
- Verify that gutters, downspouts, and French drains route water away from the slab, guaranteeing proper drainage.
- Conduct annual infrared scans to spot hidden moisture before it compromises structural integrity.
Addressing Cracks: A Step-by-Step Repair Process
When a crack appears, immediate action limits structural damage:
- Map crack width and length.
- Perform ground-penetrating radar to check for underlying voids.
- For widths under 0.25 mm, inject a low-viscosity epoxy resin.
- For wider gaps, chase-cut the joint, add carbon-fiber stitching if load demands warrant, then fill with a flexible polyurethane sealant.
- Grind flush and polish so forklifts glide smoothly over the repair.
Average repair costs in Beaumont, TX range from $4 per linear foot for micro-injection to $22 for stitched structural rehabilitation—still far less than full slab replacement or the operational downtime that comes with it.
Why Superior Grouting Is Trusted Across Southeast Texas
From petrochemical refineries along the Sabine-Neches Waterway to logistics hubs in Houston, facility engineers choose Superior Grouting because our evaluation and repair services combine laser-guided surveying, high-density polyurethane foam, and long-track records of success. Whether the project calls for foam injection beneath a loading dock, concrete leveling for a warehouse expansion, or joint sealing on a tarmac, we deliver precision results that withstand demanding Gulf Coast conditions.
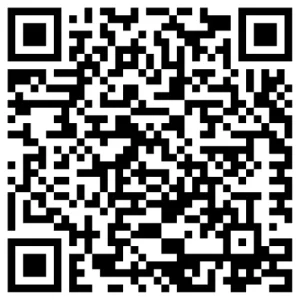