Does Self-leveling Concrete Crack Over Time in Houston, TX?
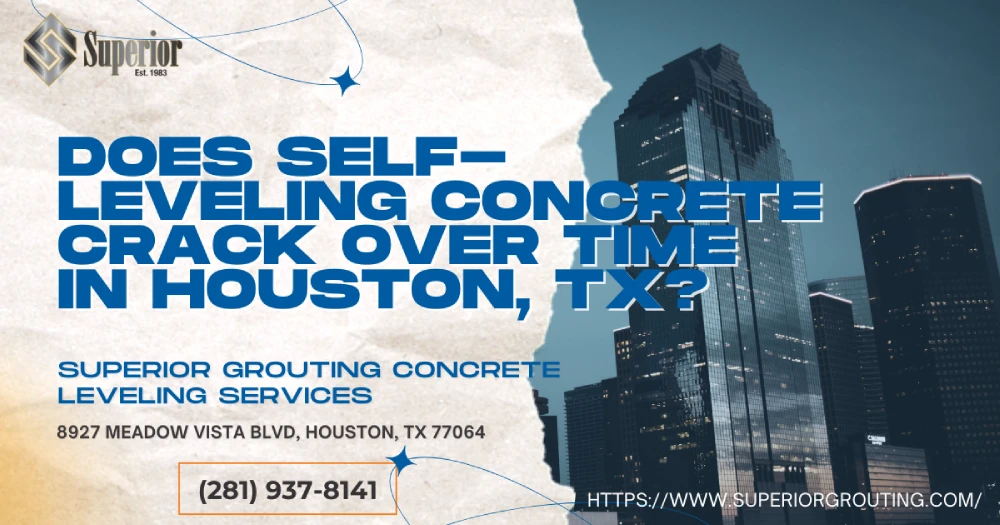
Self-leveling toppings promise a flawless finish, yet even the slickest pour can fracture if Gulf Coast variables go unchecked. Extreme temperature swings, high humidity, soil settlement, and heavy industrial traffic all conspire to stress a new concrete slab. The good news? Careful prep, the right self-leveling compound, and proven concrete leveling solutions—whether traditional concrete leveling, polyurethane foam injection, or PolyLevel—can keep slabs of concrete flat, safe, and strong for decades.
Below, you’ll discover what causes cracking, how to level your concrete properly, and ways to prevent future movement in the Houston area. Expect practical advice backed by manufacturer’s instructions, not marketing hype.
Concrete Level Challenges Unique to Houston, TX
Houston’s expansive clay soils expand when wet and contract when dry, producing voids underneath the concrete. Heavy rainfall can seep through joints, erode sub-grade, and compromise support. When the soil settles, slabs become uneven, creating dips, trip hazards, and hairline fissures that telegraph to finished surfaces such as tile. Add triple-digit heat, high nighttime humidity, and accelerated wear and tear from machinery, and you have a recipe for cracks—unless slabs are properly stabilized.
Substrate Preparation: The First Line of Defense
A self-leveling pour is only as stable as the substrate beneath it. Industry-approved steps include:
- Inspect and document early signs of damage. Look for spalls, surface delamination, and debris and dust that can weaken bond strength.
- Grind or shot-blast to the specified Concrete Surface Profile (CSP) so primer can penetrate.
- Vacuum small holes and voids, then seal oil stains.
- Route hairline cracks and fill them with epoxy or semi-rigid sealant.
- Prime according to the manufacturer’s instructions within 24 hours of the pour to reduce pinholes and enhance adhesion.
Skipping any of these steps leaves micro-pockets where moisture can collect, leading to soil erosion and slab movement down the road.
Choosing the Right Self-Leveling Compound or Concrete Mix
Not all bag mixes cure the same. For facilities in TX, look for a polymer-modified self-leveling compound formulated for high humidity, high temperature, and rapid strength gain. Key features include:
- Low-shrink cement chemistry to reduce curling
- Fiber reinforcement to arrest micro-cracks
- Working time long enough to spread evenly with a gauge rake or squeegee without tearing
- Compatibility with primers, sealants, and coatings you plan to install
Polymer additives boost flexural strength, helping the material resist dynamic loads from forklifts or cranes. If an overlay must reach 6,000 psi compressive strength, verify test data before ordering pallets.
Application Techniques That Keep Slabs Level and Crack-Free
- Control water content. Over-watering the mix increases bleed water and plastic-shrinkage cracks.
- Pour self-leveling concrete in a continuous wet edge; staggered batches create cold joints that later turn into faults.
- Use a trowel or spiked roller to break surface tension and allow trapped air to escape.
- Maintain ambient moisture levels with curing compounds or light misting so the surface doesn’t dry faster than the interior layer.
- Restrict vibration, foot traffic, or equipment movement until the overlay reaches design strength.
By following these steps, you create a smooth, uniform finish and limit long-term maintenance calls.
When Self-Leveling Alone Isn’t Enough: Concrete Lifting & Leveling in Houston
Some facilities pour an overlay only to watch it crack again because the underlying slab keeps sinking. In these cases, lifting the concrete before resurfacing is essential. Three primary methods are used in the Houston area:
1. Polyurethane Foam Injection (PolyLevel)
PolyLevel uses expanding polyurethane foam to fill voids beneath the concrete. The material is lightweight, cures rapidly, stabilizes the soil, and provides minimal disruption to ongoing operations. Technicians drill small holes, inject the foam, and monitor lift in real time. The foam expands, compacts the soil, and raises the slab to the desired level.
Advantages:
- Non-invasive and environmentally friendly
- Ready for traffic in 15 minutes
- Won’t add excess weight that could worsen soil settlement
2. Traditional Concrete Leveling (Mudjacking)
Mudjacking pumps a slurry of cement, sand, and water beneath the slab that needs lift. The mixture fills voids and raises the surface, but its heavier weight can sometimes lead to further settlement on weak sub-grade.
3. Self-Leveling Overlay After Lifting
Once the slab is returned to grade, a thin self-leveling topping can be installed to create a perfectly smooth finished floor.
Selecting the best concrete lifting technique depends on load, soil conditions, budget, and required cure time. A reputable contractor can provide a free concrete leveling estimate that compares each option.
Curing, Sealing, and Joint Design to Prevent Future Cracks
After leveling concrete, proper curing and sealing lock in durability:
- Maintain slab temperature between 60–80 °F for 72 hours.
- Apply a penetrating sealer to reduce moisture intrusion and oil staining.
- Saw-cut control joints at 25–30× the overlay thickness to channel shrinkage and prevent random cracks.
- Seal expansion joints with elastomeric products that accommodate movement and block drainage water from seeping beneath the concrete.
Following this regimen decreases the chance that cracks will widen or new dips form due to erosion or soil movement.
Common Causes of Cracking Months or Years Later
Even a well-poured self-leveling surface can crack over time if:
- Heavy point loads exceed slab design strength.
- Moisture migrates from underneath the concrete and raises vapor pressure.
- Drain lines clog, leading to ponding water that compromises support.
- Soil settlement undermines one corner, causing differential lift.
- Sealant fails and allows contaminants to attack the bond line.
Periodic inspections allow maintenance teams to mark any hairline fissures, inject epoxy before they expand, and keep traffic rolling safely.
Proactive Maintenance to Extend Slab Life
- Keep drainage systems clear so runoff can’t erode the sub-grade.
- Check joint sealant annually and replace if it hardens or debonds.
- Monitor low spots and schedule leveling concrete repairs before forklifts start rocking.
- Use non-corrosive de-icers to avoid chemical attack on concrete surfaces.
- Review operational changes—added racking, heavier equipment, or new production lines—and upgrade slab reinforcement if loads will increase.
Commit to these measures and you’ll dramatically reduce life-cycle costs on high-traffic concrete floor systems.
Key Takeaways for Managers in the Houston Area
- Self-leveling concrete can crack, but only when substrate prep, curing, and soil stabilization are ignored.
- Understanding local soil behavior and moisture levels is critical before choosing a self-leveling compound or foam injection solution.
- Combining polyurethane lifting, precise leveling compound placement, and robust sealing creates a resilient, long-lasting floor.
- Partner with a contractor experienced in concrete repair, concrete lifting, and slab stabilization for minimal downtime and maximum ROI.
Need more guidance? Contact Superior Grouting for an on-site evaluation and a free concrete leveling estimate tailored to Gulf Coast conditions.
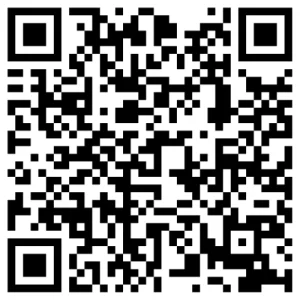