What Is the Method of Cement Stabilization in Houston, TX?
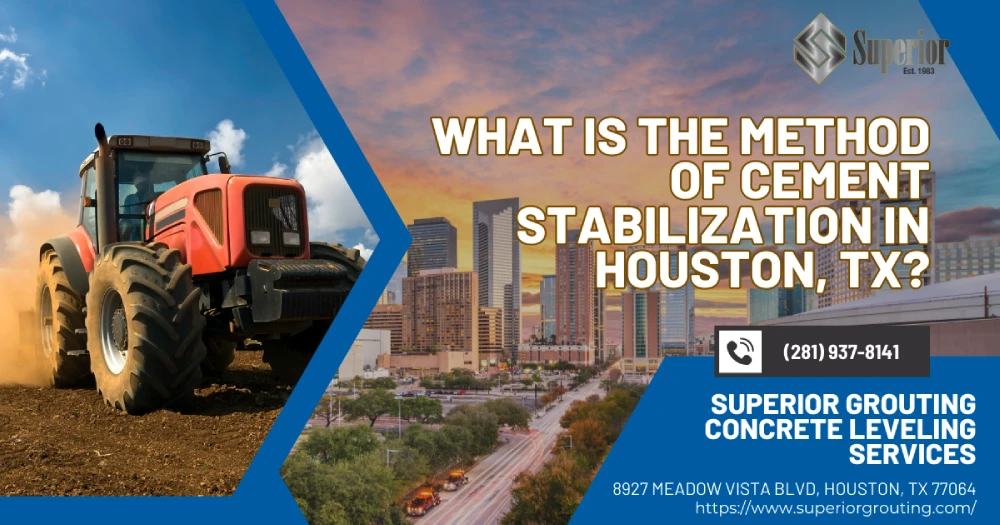
Every construction team operating along the Texas Gulf Coast eventually confronts the same challenge: clay soil that loves to expand and contract with every change in moisture. Left untreated, this movement weakens the foundation of industrial warehouses, logistics yards, and highway pavement, leading to premature cracking, rutting, and costly repairs. An experienced soil stabilization contractor solves the problem by blending carefully measured additives—chief among them Portland cement—directly into the existing soil. The result is a strong and stable subgrade that can withstand the weight of heavy truck traffic and large structural loads.
Although multiple types of soil stabilization exist, cement stabilization dominates in the Houston area because it delivers rapid strength gain, high bearing capacity, and outstanding durability against Gulf Coast weather. Below, we walk through the complete soil stabilization process, compare it with lime stabilization and fly ash soil stabilization, and explain why partnering with a reputable stabilization company such as Superior Grouting can make—or break—your next infrastructure or industrial facility project.
Key Takeaways
- Cement Stabilization Tackles Expansive Clays: Cement stabilization transforms Houston’s moisture-sensitive clay soils into solid, load-bearing platforms. By minimizing soil expansion and contraction, it prevents pavement cracking, foundation damage, and costly repairs across industrial, infrastructure, and heavy construction projects.
- Data-Driven Soil Analysis Ensures Accuracy: Every project starts with soil classification and lab testing to determine plasticity, moisture content, and required strength. This allows engineers to tailor cement percentages precisely, ensuring long-term durability and avoiding under- or over-treatment.
- Precise Mixing and Compaction Are Critical: Cement and soil are blended on-site using reclaimers and moisture conditioners, then compacted to exact density levels. This creates a uniform, stabilized layer ready for pavement, reducing delays and preventing weak zones that could later fail.
- Cement Outperforms Lime and Fly Ash Alone: While lime lowers plasticity and fly ash adds durability, cement provides faster strength gain and early load capacity. In Houston’s wet climate, cement or cement-lime blends are preferred for time-sensitive and heavy-load applications.
- Cost-Effective and Environmentally Smarter: In-place stabilization with 4–8% cement reduces excavation, truck hauls, and aggregate demand—cutting emissions up to 40%. Over decades, this method proves more sustainable and economical than removing and replacing expansive or unstable soils.
- Injection Stabilization Fixes Local Failures Fast: For post-construction issues, high-pressure cement-lime injection fills voids beneath slabs without excavation. It restores load-bearing support quickly, keeping industrial facilities and logistics operations running with minimal downtime or disruption.
1. Site Investigation and Soil Classification
Every successful stabilization project starts with data. Geotechnical technicians collect bulk samples of the existing soil along planned alignment corridors, then test for:
- Plasticity Index (PI) to gauge clay content and swelling potential
- Optimum moisture content and dry density for compaction
- Acid-base balance, sulfates, and organic matter that might inhibit a chemical reaction
High PI values (often 25–45 in Gulf Coast clays) indicate the need for stronger additives like cement or a cement-lime blend. By knowing precisely which type of soil you are treating—fat clay, lean clay, silty clay—you can select the best soil stabilization method and dosage.
2. Calculating the Correct Cement Percentage
Laboratory tests such as unconfined compressive strength (UCS) and Eades & Grim pH checks establish the minimum amount of additive needed to reach project targets—commonly 300–400 psi UCS for heavy haul roads. For most Houston clays, engineers specify between 4 % and 8 % cement by dry soil weight. Adding more than required increases brittleness; adding less risks insufficient shear strength.
When the PI is extremely high, designers often call for a two-stage treatment: 2 % lime to reduce plasticity and mellow the clay, followed by 4–5 % cement to lock particles into a dense, water-resistant matrix. This blended approach is still considered cement soil stabilization because cement produces the bulk of ultimate strength.
3. Precision Spreading of Additive
Modern projects use computer-controlled spreaders to place cement—or a cement/fly-ash blend—at an exact pounds-per-square-yard rate. Accurate distribution prevents soft spots, ensures uniform curing, and eliminates wasted material. Good spreader practice means starting and stopping outside the treatment zone so the surface receives one even application.
4. In-Place Mixing and Moisture Conditioning
A reclaimer-stabilizer pulverizes soil to the specified depth—often 8 to 12 inches—spraying just enough water to bring the blend within ±2 % of optimum moisture. Proper hydration activates the cement’s binder chemistry and allows compaction crews to reach 95 %–97 % of standard Proctor density. Because hydration starts immediately, crews must compact the treated lift while it still feels workable. Delays can create hard lumps that fail density tests.
5. Compaction and Grading
Padfoot rollers provide high energy to seat the treated soil, followed by pneumatic or smooth-drum rollers that seal the surface. Final grading blades shape the stabilized layer to design elevation so later asphalt paving or rigid pavement goes down smoothly. Technicians verify quality with nuclear density gauges and field UCS cylinders.
6. Curing and Protection
Cement-treated soil needs moisture to finish hydrating. Light, frequent water spray for three to seven days prevents surface drying and dusting. Once the UCS meets specification, the layer can accept overlying base rock, hot-mix asphalt, or directly support a concrete pavement—a schedule advantage that saves days compared with remove-and-replace excavation.
How Cement Stabilization Compares to Lime and Fly Ash Treatments
- Lime stabilization excels at lowering PI and reducing swelling in high-plasticity clays but gains strength more slowly than cement. On projects requiring early trafficking, adding cement or a lime-cement blend is preferred.
- Fly ash stabilization involves Class C or Class F fly ash. Class C is self-cementing and pairs well with clay soils to increase durability while lowering total cement demand and greenhouse-gas footprint.
- Using fly ash as a partial substitute can improve sulfate resistance, making it valuable on the Gulf Coast where brackish groundwater may introduce aggressive ions.
Ultimately, the best choice depends on site chemistry, timeline, and performance criteria. An experienced soil stabilization company can run trial mixes to confirm which additive combination offers optimum load-bearing capacity and long-term durability.
Benefits of Cement-Treated Subgrades for Heavy Construction Projects
- Higher bearing capacity and lower compressibility allow designers to reduce imported aggregate thickness, cutting truck traffic and fuel consumption.
- The hardened matrix blocks erosion and weathering, increasing pavement life cycles by five to ten years.
- Contractors save time and money by stabilizing in place rather than hauling off thousands of cubic yards of unstable soil. Fewer trucks on the road mean lower emissions and safer construction sites.
- Because stabilized soil resists moisture fluctuation, it keeps industrial floors and roadway surfaces level, reducing long-term repair costs associated with differential settlement.
Environmental and Cost Considerations
Critics sometimes point to the embodied CO₂ of Portland cement. However, replacing full-depth excavation with a 4 % cement treatment typically cuts total project emissions by 30 %–40 % thanks to fewer truck trips and minimal aggregate mining. Over a 30-year analysis period, cement stabilization emerges as one of the most cost-effective and sustainable ground-improvement options available in the Texas construction market.
Injection Stabilization for Localized Troublespots
While large footprints favor in-place mixing, some facilities encounter isolated pockets of unstable soil after construction is complete. For those locations, Superior Grouting offers high-pressure cement-lime injection stabilization. Crews drill small-diameter holes through the slab, pump a flowable grout that penetrates voids, then hardens to re-establish load-bearing contact. Injection avoids disruptive excavation and keeps plants running with minimal downtime.
Choosing the Right Soil Stabilization Contractor in Houston
Cement treatment is equal parts science and craftsmanship. Selecting a proven soil stabilization contractor ensures:
- Access to high-output spreaders, reclaimers, and rollers sized for large-scale construction projects
- A qualified field laboratory that can adjust cement, lime, or fly ash ratios on the fly
- Strict documentation of additive rates, field densities, and UCS results to protect project warranties
Superior Grouting has delivered turnkey stabilization services in Houston for decades. Our crews understand Gulf Coast rainfall patterns, traffic control requirements, and the importance of meeting TxDOT or industrial specifications the first time. Whether your project involves new port infrastructure, distribution centers, or energy corridors, we can stabilize the soil quickly so vertical construction stays on schedule.
Conclusion: Strong, Stable, and Built to Last
Houston’s expansive clay soils don’t have to derail schedules or inflate budgets. By following a disciplined stabilization process—site investigation, correct cement dosing, precise mixing, rapid compaction, and diligent curing—contractors create a durable, load-bearing platform that stands up to heavy equipment, Gulf Coast storms, and decades of service. Add professional quality control and the method becomes a reliable foundation strategy that outperforms simple excavation or short-term chemical fixes.
If your next infrastructure build demands a subgrade that resists moisture, erosion, and repetitive loads, talk to a trusted stabilization company about cement stabilization. The investment today can spare you from unexpected downtime, premature resurfacing, and the spiraling expenses tied to untreated expansive soil tomorrow.
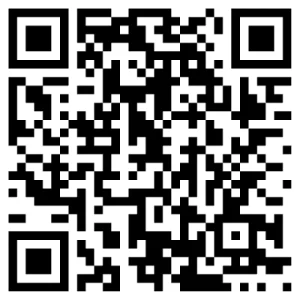