What Is the Use of Polyurethane Grout in Houston, TX?
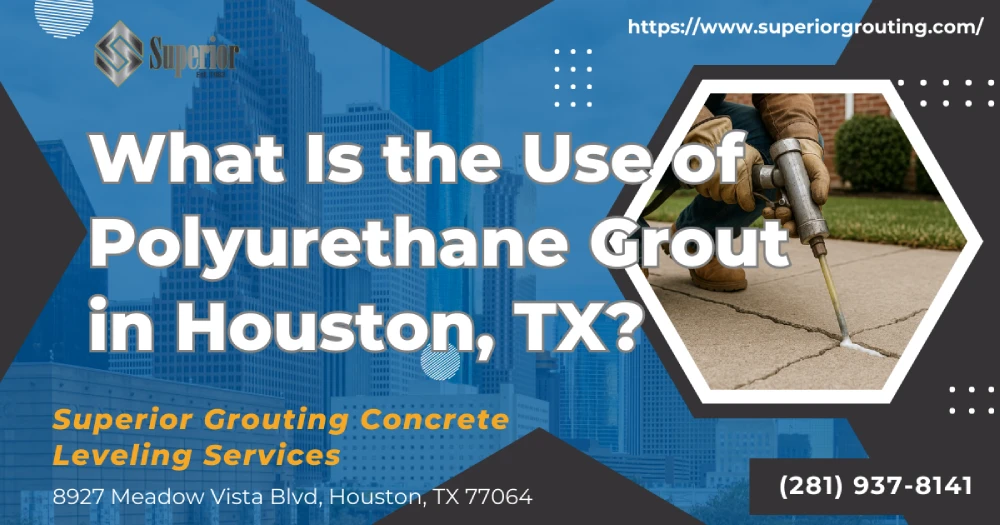
In Houston, TX, polyurethane grout is primarily used for foundation repairs, soil stabilization, and large-scale infrastructure projects. The fast-expanding resin offers an effective method for lifting and leveling concrete slabs, sealing active leaks, and reinforcing weak Gulf-Coast soils—all while minimizing downtime and disruption to critical operations.
Key Takeaways
- Polyurethane grouting is a hydrophobic, cost-effective solution that expands rapidly to fill voids, stabilize soil, and stop water ingress.
- Houston’s hot, humid climate and soft coastal clays make polyurethane foam the preferred material over cement grouts and epoxies.
- Common applications include roadway slab jacking, tunnel leak sealing, and industrial foundation repair where minimal excavation is required.
- Properly executed polyurethane injection can save 40–70 % versus full replacement while adding decades of service life.
- Always choose a certified contractor experienced in high-groundwater environments to ensure reliable results.
Understanding Polyurethane Grout and How It Works
Polyurethane grout—sometimes called polyurethane foam, injection resin, or simply “polyfoam”—is delivered as two liquid components that mix at the pump and expand aggressively once they contact water or air. As the foam expands, it fills cracks, seeks out water pathways, and bonds to concrete substrate or surrounding soil particles. When cured, the hardened material forms a closed-cell matrix that resists erosion, chemical attack, and future water penetration.
Key Properties
- Expansion Ratio: 10–30× original liquid volume
- Initial Reaction: 3–15 s after mixing
- Compressive Strength: 50–3,000 psi depending on formulation
- Density Range: 2–20 lb/ft³, allowing lightweight void filling or high-density structural stabilization
- Water Tolerance: Hydrophobic chemistry actively chases and displaces water
Because the foam chases moisture, polyurethane injection is uniquely suited for Houston facilities constantly battling high groundwater tables or tidal influences.
Core Industrial Applications Across Houston
1. Leak Sealing in Concrete Tunnels and Utility Vaults
Underground tunnels, clarifiers, and manholes frequently develop leaks at joints or penetrations. Polyurethane grouting travels along the leak path, expands, and hardens into a watertight curtain that blocks infiltration instantly—far faster than traditional cement grouting.
2. Foundation Repair and Soil Stabilization
Refineries, chemical plants, and port facilities often rest on soft, moisture-sensitive soils. By injecting high-density polyfoam beneath footings, engineers can increase bearing capacity, stop settlement, and prevent differential movement without shutting down operations.
3. Lifting and Leveling Concrete Slabs
Polyurethane slab jacking is a minimally invasive alternative to slab replacement. Crews drill ⅜-in. ports, inject foam beneath the concrete slab, and watch as it gently lifts, levels, and re-establishes design elevations—perfect for loading docks, warehouse floors, and runway panels.
4. Void Filling Under Roadway and Rail Corridors
Washouts, abandoned pipes, and collapsed culverts create hidden cavities that jeopardize public safety. Lightweight polyurethane foam fills those voids completely, reduces hydrostatic pressure, and prevents future sinkholes, all while keeping highway or track downtime to a minimum.
5. Erosion Control Along Bulkheads and Seawalls
Storm surge and tidal action scour soils behind waterfront structures. Polyurethane injection compacts loose materials, fills voids, and forms a waterproof barrier that mitigates future erosion—an environmentally responsible alternative to large-scale rip-rap replacement.
Why Houston’s Climate Favors Polyurethane Grouting
High Groundwater and Heavy Rainfall
Houston averages more than 50 in. of rain each year, and subsurface groundwater routinely sits within a few feet of grade. Hydrophobic polyurethane foam continues to expand in the presence of water, making it ideal for leak sealing and soil stabilization where cement or epoxy grouts struggle.
Expansive Clays and Subsidence
Gulf-Coast clays expand when wet and shrink during droughts, causing pavement heave or settlement. Polyurethane’s flexible, closed-cell structure tolerates minor movement while supporting full structural loads.
Extreme Temperatures and Humidity
With summer heat indices topping 110 °F, many chemical grouts have cure issues. Polyurethane maintains predictable reaction profiles from 40 °F to 120 °F, so crews can work nearly year-round without performance loss.
Step-By-Step Polyurethane Injection Process
Site Evaluation
- Ground-penetrating radar and core samples locate voids, water flow, or weak soil zones.
- Engineers determine the correct foam density, viscosity, and set time for each location.
Drilling and Port Installation
- Technicians drill ⅜ – ⅝-in. holes on a grid pattern.
- Mechanical or hammer-in ports are inserted to guide the grout beneath or behind the concrete slab or structure.
Injection, Expansion, and Monitoring
- A proportioning pump meters equal parts “A” and “B” into a static mixer.
- The blended grout is injected; expansion pressure gently lifts the slab, compacts soil, or fills the void.
- Crew monitors elevation with laser levels and checks back-pressure to verify full compaction.
Quality Assurance
- Infrared thermography confirms heat signature of complete foam spread.
- Dynamic cone penetrometer tests verify soil densification.
- Any soft spots are re-injected on the spot.
Clean-Up and Return to Service
- Ports are removed or cut flush; drill holes are patched with non-shrink cement.
- Most slabs and structures return to full load capacity within one to two hours.
Polyurethane vs. Traditional Cementitious Grouts
Property / Goal | Polyurethane Grout | Cement Grout
Reaction Time | Seconds | Minutes to Hours
Water Tolerance | High (hydrophobic) | Moderate
Excavation Needed | Minimal | Often Extensive
Density Control | 2–20 lb/ft³ | ~120 lb/ft³
Slab Return-to-Service | 1–2 h | 24–48 h
Environmental Impact | Closed-cell, inert | Higher embodied carbon
Between the faster schedule, lower logistics costs, and reduced carbon footprint, polyurethane grouting is frequently the most cost-effective choice for Houston’s high-traffic industrial corridors.
Cost and ROI Considerations
Although polyurethane resin costs more per gallon than cement slurry, overall project budgets are typically 40–70 % lower when factoring:
- Reduced labor hours (smaller crew, faster cure)
- Virtually no excavation or concrete demolition
- Minimal traffic control and lane closures
- Longer design life and fewer repeat repairs
Plants, ports, and DOT agencies often realize full return on investment in less than a year through decreased water-treatment fees, extended pavement life, and improved operational uptime.
Sustainability and Environmental Benefits
- Polyurethane foam is solvent-free and VOC-compliant.
- Closed-cell structure prevents leaching and resists erosion, reducing future material demand.
- Projects may qualify for LEED or Envision credits under Existing Infrastructure Reuse and Whole-Life Carbon Reduction.
- Lightweight void filling reduces truckloads of cement and aggregate, lowering greenhouse-gas emissions tied to material haul-in/haul-off.
Selecting a Qualified Polyurethane Grouting Contractor
Certifications
- ICRI Concrete Repair Certified
- AMPP or NACE coatings inspection credentials for concrete-to-steel interfaces
- OSHA confined-space entry program with EMR below 1.0
Proven Local References
- Ship-channel bulkhead stabilization under tidal conditions
- Light-rail track compaction completed during overnight windows
- Petrochemical containment dike leak sealing performed without production shutdown
Transparent Testing and Reporting
- Before-and-after slab elevations, soil modulus, and infiltration rates
- Written warranty covering both material and workmanship
Conclusion
Polyurethane grouting delivers Houston’s infrastructure owners a fast, durable, and environmentally responsible method to stabilize soil, lift concrete slabs, seal leaks, and combat erosion—without lengthy shutdowns or massive excavation. The foam’s ability to expand, compact, and harden in high-groundwater environments makes it uniquely suited for the Gulf Coast. When executed by certified professionals, polyurethane injection offers a cost-effective path to decades of additional service life for foundations, roadways, and critical industrial assets.
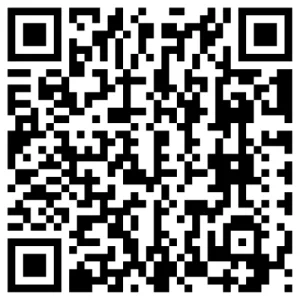