When Should You Not Use Self-Leveling Concrete in Beaumont, TX?
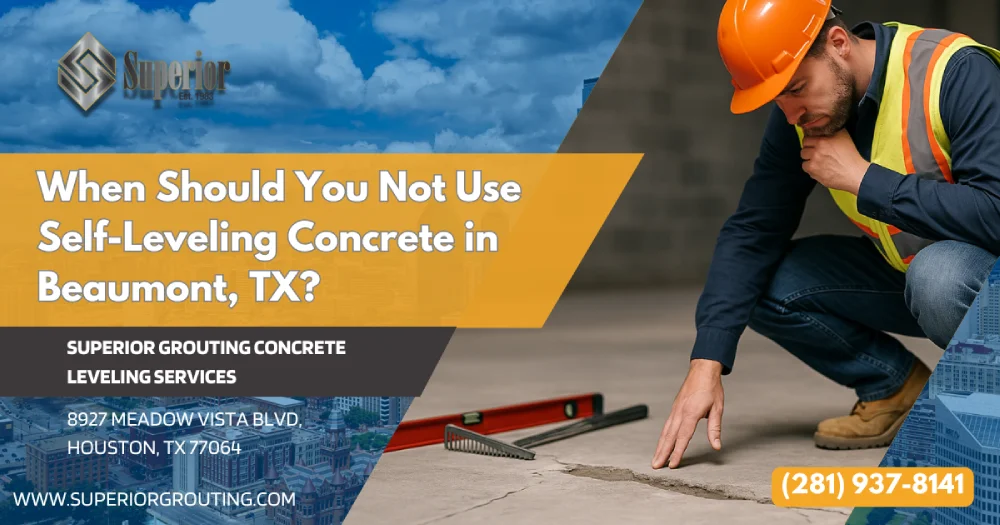
Self-leveling concrete is often marketed as the “quick fix” for uneven concrete slabs, but the product comes with limits—especially in Beaumont, TX and surrounding Gulf-Coast markets where humidity, temperature spikes, and aggressive industrial traffic push materials to their breaking point. Understanding when to step back and specify a different repair—whether that’s poly concrete raising, full-depth concrete lifting, or a bonded overlay—will save money, reduce downtime, and protect the long-term integrity of structures in Beaumont.
Key Takeaways
- Self-leveling toppings work only on sound, stable substrates that show minimal flex.
- Beaumont’s coastal climate generates high moisture vapor that can blister or delaminate thin, dense toppings
- Heavy forklifts, steel wheels, and constant vibration exceed the abrasion limits of standard self-levelers—opt for polymer-modified or epoxy materials instead.
- Depth limitations matter: most mixes cap at 1” neat or 5” with clean aggregate. Deep repairs should be handled with concrete lifting or grout fills before any finishing course.
- The City of Beaumont permit requirements of this code may trigger additional inspections if you cover expansion joints or raising services alter drainage pathways.
Beaumont’s Climate: Why It Challenges “Flowable” Leveling Products
Leveling in Beaumont isn’t as simple as choosing a bag mix and adding water. The region’s humidity often pushes in-slab relative humidity (RH) beyond 90 %, and summertime deck temperatures can climb past 100 °F.
- Moisture Vapor Transmission
– The dense matrix of self-leveling concrete limits vapor escape. When Beaumont’s slab RH exceeds 75 %, vapor pressure builds, resulting in pinholes or bond failures. - Sudden Temperature Swings
– Gulf storms can drop ambient temperature by 15 °F in an hour. Rapid cooling shrinks the topping faster than the substrate, introducing shear stress. - Wind-Driven Rains
– Storm events tied to the Texas Windstorm Inspection Program can saturate outdoor concrete surfaces. Because self-levelers lack entrained air, they scale under freeze-thaw and wet-dry cycling.
Structural Conditions That Disqualify Self-Leveling Concrete
Wide or Moving Cracks
Self-leveling toppings are rigid. If the underlying concrete surface shows differential movement of 1/8” or more—or if active joints continue to widen—cracks will telegraph through the overlay. In these cases, consider poly concrete leveling or traditional concrete repair methods approved by the International Building Code and relevant sections of the International Residential Code.
Heavy-Load Traffic and Impact Zones
Beaumont’s refineries, fabrication shops, and warehouse corridors routinely carry axle loads well above 3,000 lbs. Standard self-leveling mixes advertise compressive strengths of 4,000–5,000 psi, but their abrasion resistance lags behind polymer-modified toppings. Areas under gantry cranes, coil storage, or steel-wheel carts need epoxy mortar or polyurethane concrete raising solutions.
Deep Depressions and Settled Concrete
When settled concrete exceeds 5” of deflection, filling with neat self-leveler makes no economic or structural sense. Instead, use concrete lifting, corsair concrete lifting foam, or poly concrete raising injections to re-support the slab. Once load transfer is achieved, a 3/8” to 1/2” self-leveler can refine the finish, but it should never be used as the primary fill.
The Economics of Industrial Floor Repairs in Beaumont, TX
Repair Method | Ideal Depth | Traffic Resistance | Typical Cure to Service | Relative Cost | Comment |
Self-Leveling Concrete | 1” neat / 5” extended | Moderate | 24–48 hrs | $$ | Great for cosmetic leveling but limited outdoors |
Poly Concrete Leveling | Void under entire slab | Excellent | 15–30 mins | $$$ | Fast return-to-service; lifts, stabilizes, seals joints |
Epoxy Mortar Overlay | 3”+ | Superior | 24 hrs | $$$$ | Handles abrasive steel-wheel traffic |
Traditional Screed | 4–6” | Good | 3–7 days | $ | Slower but proven under bulk storage loads |
City of Beaumont Codes, Permits, and What “Permits Shall Not Be Required” Really Means
Contractors occasionally assume that thin toppings bypass local regulations because “permits shall not be required” for cosmetic repairs. In reality, the ordinances of this jurisdiction reference both the International Building Code and the International Residential Code, and the code council has clarified that work impacting structure, drainage, or egress still triggers review.
Key points:
- If concrete raising alters slope toward drains regulated by the city of Beaumont, a permit may be mandatory.
- The Texas Windstorm Inspection Program governs wind-borne debris zones, even for slabs supporting rooftop mechanical equipment.
- Failing to log a repair can void certain warranty claims related to foundation repair or later structural enhancements.
Always verify with local officials before scheduling leveling services.
Depth & Profile Constraints Specific to Leveling Beaumont-Area Facilities
- Maximum Single-Lift Thickness
Most manufacturers cap neat pours at 1”. Beaumont’s heat accelerates hydration, increasing the risk of surface tearing. Extension mixes (3/8” aggregate) allow up to 5”, but shrinkage doubles. - Curling & Edge Lift
Self-levelers shrink more than conventional concrete slabs. On large warehouse panels, edges can lift 1/16” or more, creating trip hazards and early joint breakdown. - Bond Requirements
– Shot-blast or scarify to a minimum CSP-4 profile.
– Use a two-part epoxy primer to overcome Beaumont’s frequent high humidity.
– Perform pull-off tests (ASTM C1583) to verify ≥175 psi bond strength.
Alternatives When Self-Leveling Concrete Isn’t the Answer
Poly Concrete Raising (Foam Injection)
Poly concrete raising delivers rapid lift, fills voids, and seals joints—making it the go-to repair when forklifts need to roll in minutes. Because the material is hydrophobic, it resists Beaumont’s ground moisture and remains stable in the presence of sulfates often found in coastal soils.
Corsair Concrete Lifting
Corsair concrete lifting is a high-density polyurethane system designed for heavy industrial settings. Unlike generic foam, it attains 8,000 psi compressive strength, making it ideal for oil-and-gas plants and port operations in Beaumont TX.
Polymer-Modified Toppings
Adding latex or acrylic polymers increases flexural strength and abrasion resistance. These toppings hit 6,000 psi compressive and can incorporate integral color or broadcast quartz for slip resistance.
Epoxy Mortar Overlays
Epoxy mortar overlays are virtually bulletproof against steel wheels, pallet jacks, and chemical exposure. While the initial cost is higher, life-cycle savings often outweigh the expense, especially when factoring the downtime costs of repeat concrete repair.
Scheduling and Environmental Control
- Avoid pouring self-leveling concrete in direct sun past 10 a.m. between May and September; slab temps exceed workable limits.
- Portable HVAC or evaporative cooling keeps ambient temp at 70–75 °F, extending working time.
- Dehumidification aids in meeting moisture-sensitive flooring specs, but in Beaumont, plan for longer dry times than the data sheet’s 70 °F/50 % RH baseline.
Life-Cycle Costing: The Long View on Leveling Services
Industrial operators in Beaumont TX demand minimal downtime. A bargain self-leveler that powders under forklift traffic after 18 months costs more than an epoxy system lasting a decade. Figure in:
- Labor & lost production during shutdowns.
- Possible code council re-inspection for every major repair.
- Future foundation repair allowances if original voids were never filled.
Conclusion
Self-leveling concrete is a remarkable product—until it meets Beaumont’s humidity, heavy loads, or deep slab voids. When any of these conditions exist, switch to concrete lifting, poly concrete leveling, or epoxy mortar overlays. The right material choice, paired with a clear understanding of city of Beaumont codes and Texas Windstorm Inspection Program requirements, secures a durable, code-compliant solution that safeguards critical operations across TX and surrounding industrial hubs.
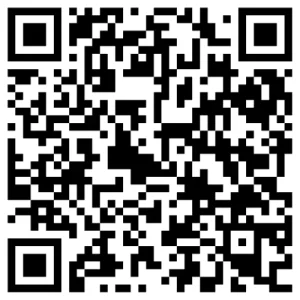