When Should You Not Use Self-leveling Concrete in Houston, TX?
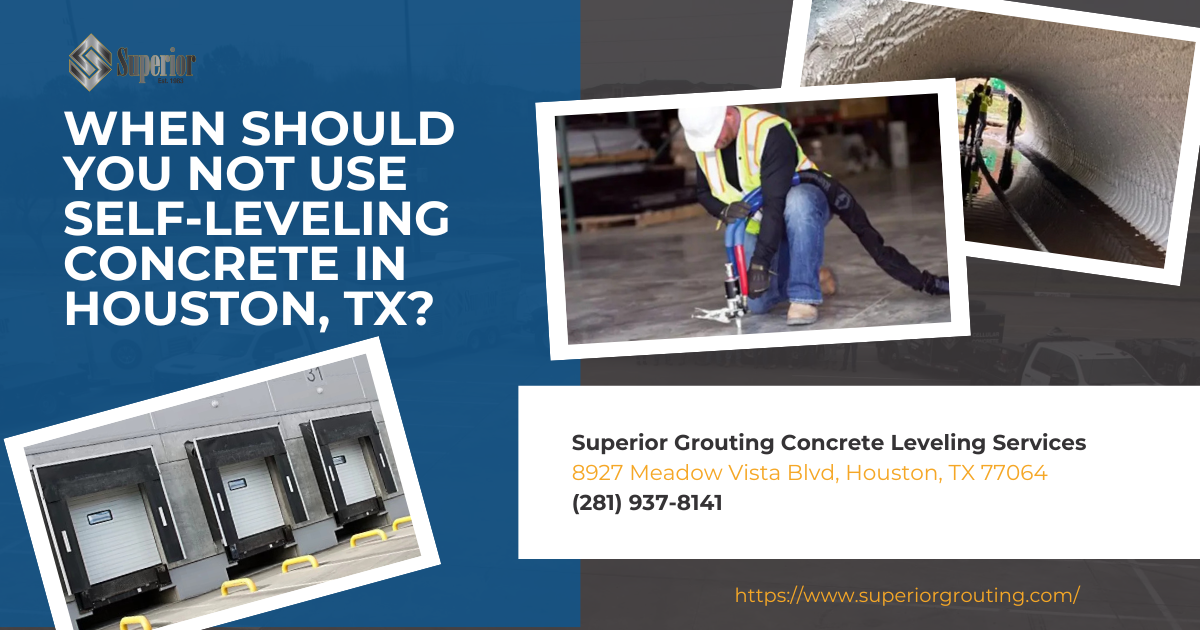
Self-leveling concrete often looks like the quickest route to a perfectly level surface. It flows, it cures fast, and it produces a smooth, laser-flat finish that makes coating crews smile. Yet Houston’s heat, humidity, and heavy industrial traffic expose limits that can turn a “simple” concrete leveling project into a costly do-over.
Before you order pallet after pallet of self-leveling compound, review the conditions that demand a different approach—whether that means a reinforced pour, polymer topping, mudjacking, polyurethane foam injection, or complete slab replacement. Understanding when to avoid self-leveling altogether protects your schedule, budget, and the long-term integrity of your concrete slab.
Understanding How Self-Leveling Concrete Works—and Where It Shines
Self-leveling concrete, also called a self leveler or self-leveling compound, is a flowable cement-based underlayment that spreads evenly across the surface with minimal screeding. Provided the floor is properly primed, the mix settles into low spots, eliminates small holes, and bonds to existing concrete to create level surfaces as thin as 1⁄8 inch and as thick as about 2 inches. The material reaches walk-on cure in a few hours, allowing coatings, tile, or other finishes to go down quickly.
For interior refurbishments—think refinishing warehouse aisles, preparing a manufacturing floor for epoxy, or correcting uneven surfaces on an old slab—self-leveling concrete frequently delivers the best results. It reduces labor costs because crews can pour self-leveling concrete, rely on gravity, and use only a gauge rake, squeegee, and straight edge to fine-tune the surface.
Red Flags: Situations Where Self-Leveling Won’t Truly Level Concrete
Despite its convenience, self-leveling isn’t magic. Houston facilities should skip it under the following conditions:
- Structural loads exceed the capacity of a 2-inch overlay.
- Outdoor exposure subjects concrete to UV, rain, and rapid temperature swings.
- Floor areas extend beyond 20,000 ft² without expansion breaks or a way to maintain a wet edge.
- Moisture vapor emissions surpass manufacturer’s instructions—usually 3 lbs/1,000 ft²/24 hr.
- Substrate movement is likely because of soil, tree roots, or ongoing settlement.
Let’s examine each scenario so you can level your concrete intelligently.
Heavy Machinery and Thick Slabs: Why Self-Leveling Concrete Falls Short
A self-leveling layer resembles underlayment, not structural concrete. Even high-performance mixes can’t match the flexural strength of a 6-inch reinforced slab or a new concrete slab with rebar. If your floor must hold racking, printing presses, or point loads from container cranes, the thin self-level surface will crack and delaminate under wear and tear. In these cases, professional concrete leveling services usually recommend one of three options:
- Traditional concrete with steel reinforcement for complete replacement.
- Steel-fiber or micro-silica toppings for medium duty upgrades.
- Polyurethane foam concrete lifting when voids beneath the slab, not the slab itself, create low areas.
Each solution adds structural capacity impossible with a 1-inch self level overlay.
Outdoor Concrete Surfaces: Houston Weather vs. Self-Leveling Compounds
Gulf Coast weather brings 100 °F pavement temps by noon, afternoon thunderstorms, and relentless UV. Self-leveling concrete and its polymers aren’t formulated for that abuse. Rapid temperature swings cause the thin layer to expand and contract faster than the concrete below, leading to hairline cracks. UV exposure bleaches the surface and weakens adhesion, while standing water can infiltrate low spots, freeze (yes, Houston has the occasional cold snap), and pop the overlay loose.
If you need level concrete in a loading dock, parking apron, or exterior mezzanine, consider:
- Air-entrained exterior-grade concrete with proper control joints.
- A silica-fume-modified mix that lowers permeability.
- A heavy-duty epoxy broadcast system installed on top of traditional concrete; the slab carries loads, the epoxy handles weather.
Massive Floors and Large Area Work: Flow Distance & Working Time Limitations
Self-levelers flow easily, but only for about 20 feet before viscosity rises. When a crew tackles a 40,000 ft² aircraft hangar or distribution center, they must establish multiple mix stations, work around columns, and keep the product moving to avoid cold joints and ridges. Logistics, not chemistry, often kill the budget. Labor costs spike as crews battle the clock to spread it evenly across the surface. Pumping rigs need water, power, and continuous material supply—resources not always available on tight industrial sites.
For large-scale concrete leveling, companies often revert to conventional screed-and-trowel concrete or semi-dry polymer screeds with longer working time. Those alternatives eliminate the risk that a self-leveling mix sets before it crosses the room.
Moisture, Humidity, and Vapor: The Hidden Enemy Beneath the Slab
Houston humidity feeds moisture vapor transmission, the silent culprit behind many concrete problems. When emissions exceed 3 lbs/1,000 ft²/24 hr (per ASTM F1869), the bond between self-leveling compound and existing concrete fails. You’ll notice blisters, pinholes, dark spots, and floor coatings coming loose. Cleaning the concrete won’t solve the chemistry issue.
Always conduct calcium chloride or in-situ RH testing. If readings are high, you may need:
- Epoxy moisture mitigation membranes for moderate vapor rates.
- A full replacement with a vapor barrier underneath the new slab.
- Mudjacking or polyurethane foam to re-support uneven concrete without capping it.
Skipping moisture tests today guarantees rework tomorrow.
Cost, Cure, and Scheduling Impacts
Bagged self-leveling material can cost $0.70–$1.10 per pound—far more than ready-mix. Add primer, stripper for residue removal, adhesion promoters, and specialized tools like a spike roller or gauge rake, and concrete costs escalate fast. Faster cure sounds nice, but remember: you still can’t set heavy equipment until strength requirements are met. High-early-strength traditional concrete often matches that timeline at a lower price per cubic yard.
When downtime dictates overnight work, self-leveling compounds can shine. Otherwise, compare total cost of ownership, including rework risk, before you commit.
Proper Preparation: The Difference Between Success and Slab Failure
Whether you decide on self-leveling concrete, polymer underlayment, or complete replacement, proper preparation rules:
- Remove oil, caulk, and residue so the leveling compound adheres.
- Shot-blast or diamond-grind to open the concrete pores and ensure proper bond.
- Prime according to the manufacturer’s instructions—skip this step and expect blistering.
- Use a screed, squeegee, and straight edge to push material into low areas.
- Break large sections of concrete into planned pours to control working time and drying time.
- Vent air bubbles with a spike roller or spiked shoes to avoid lumps.
Rushing prep because “the product is self-leveling” is the fastest route to uneven areas and early failure.
Choosing the Right Concrete Repair Strategy
No single product solves every leveling issue. A smart contractor evaluates the existing concrete, load demands, and environmental exposure before specifying:
- Self-leveling concrete to fix minor low spots on indoor floors.
- Polymer screeds for underlayment that needs extra flexural strength.
- Mudjacking to re-support settled pads without replacing them.
- Polyurethane foam injection to raise a slab that has become uneven due to voids.
- Full replacement when structural issues threaten safety.
When you work with Superior Grouting, our engineers review data—humidity tests, load charts, slab thickness—before recommending concrete leveling services. The goal is a long-term, level, trouble-free floor, not just a quick cosmetic fix.
Conclusion
Self-leveling concrete is a valuable tool, but it’s not the answer everywhere. Houston’s punishing climate, heavy equipment, large footprints, and moisture issues demand that you select the right method—sometimes that’s a thick reinforced pour, polymer topping, or polyurethane foam rather than a thin layer of self-leveling concrete. Proper preparation, accurate testing, and realistic scheduling keep your project on budget and out of the rework zone. If you’re unsure which path suits your facility, contact us today.
Superior Grouting will evaluate your site and deliver a solution that stands level, cures correctly, and stays productive for years.
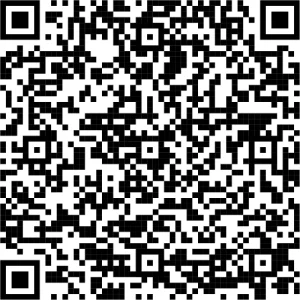